PROTOTYPE TO PRODUCTION

Protocast Inc. and Rapid Prototyping
While the process of creating prototypes is often a complicated and complex one, the concept behind the work we do here at Protocast Inc. is actually fairly simple. While we’re a full-service machine shop here in the Denver area, we specialize in rapid prototyping services that offer a number of benefits for many different types of businesses.
Design Verification
To help give your company a competitive edge when you’re transitioning from product design to manufacturing, rapid prototyping helps you save time and money. The main benefit of prototyping lies in design verification, which provides the opportunity to identify any potential design flaws before a product goes into full-scale production. This is incredibly important because the further along in the developmental cycle these errors are discovered, the greater the cost is to fix them. Certain die cast components can be especially costly, with tooling prices often running into six figures.
Prototyping Die Cast Parts
By accurately creating an exact prototype of your die-cast design, you’ll be able to discover any errors before multiple products are created. Again, the cost of discovering any design errors after the die cast tooling process is complete can be financially devastating for a business. Tool rework is an obvious cost, but additional costs can include shorter tool life and late delivery of a company’s product to the marketplace. A delay in introducing a product to the market can result in a loss of sales and even a loss of gross market share that can be difficult to recover from. So, appropriate use of today’s prototyping technologies can help manufacturers avoid these needless additional costs and stressful financial situations.
Casting With Aluminum
At Protocast Inc., what you’ll notice is that we offer multiple types of alloys that we work and cast with. These alloys include aluminum, magnesium, and zinc, and each type of alloy includes different grades of metal that are suited for specific prototyping jobs. Aluminum is a popular choice for metal casting, tooling, and manufacturing in general, as many components in the automobile, aerospace, defense and construction industries utilize aluminum for its durable yet cost-effective qualities. Even furniture can be created with cast aluminum!
Why Cast Aluminum?
Cast aluminum is used in an incredible number of different objects and applications, and we didn’t even mention cookware or boat parts. To reiterate, casting aluminum makes the raw metal extremely strong and durable. Though cast aluminum is not quite as strong as cast iron, it is very close in its strength and can be more cost-effective for a large production run. Indeed, cast aluminum can be purchased at a cost of roughly half of what you might spend on other types of metals. The lightweight properties of aluminum are also notable, making it relatively easy to work with in a manufacturing environment.
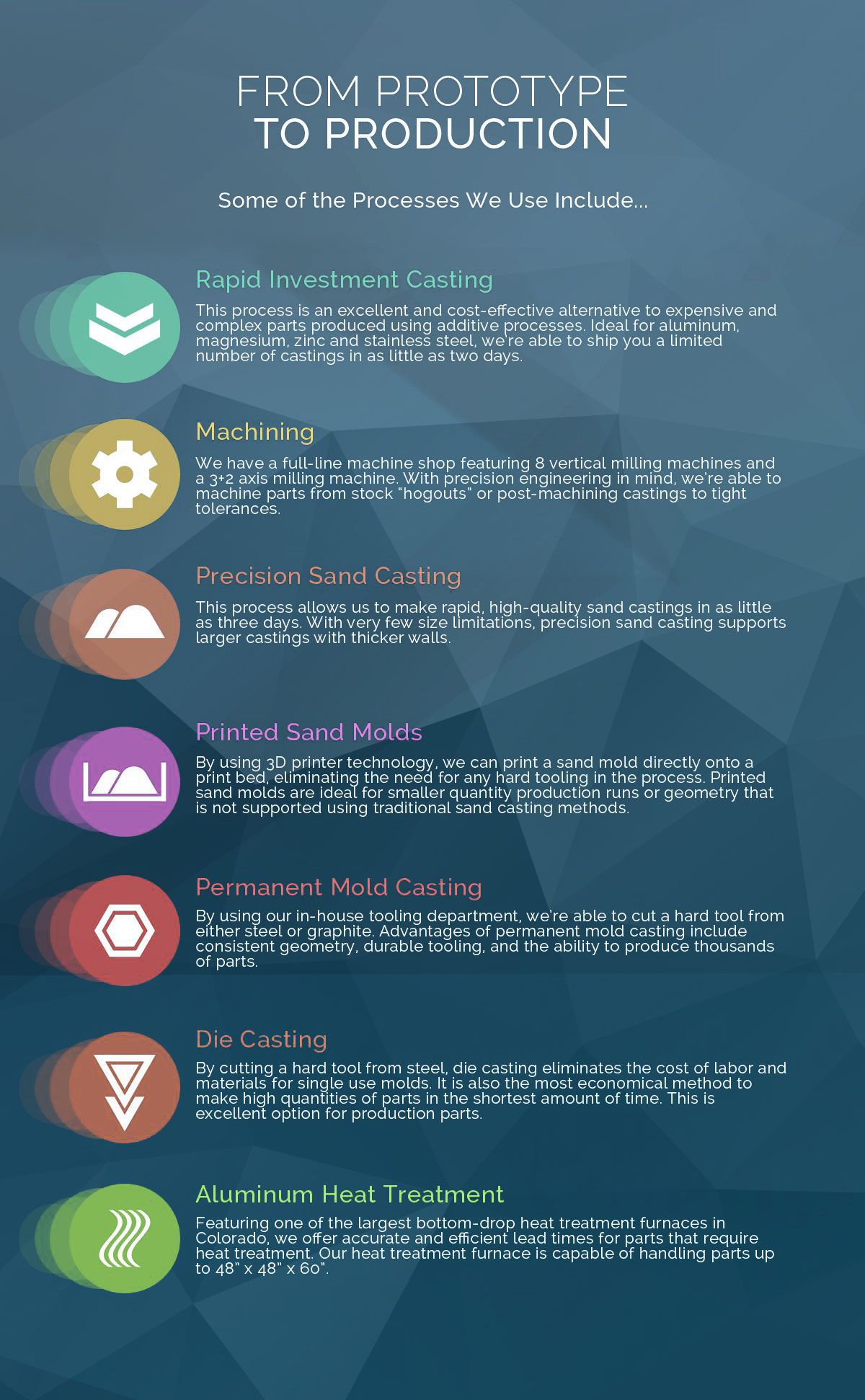
Recycling Aluminum Die Castings
Aluminum castings made here in North America are highly recyclable. Indeed, over 95 percent of aluminum castings made in our home continent are made out of post-consumer recycled aluminum. As it turns out, there is very little functional difference between primary (extracted or pure) and secondary (recycled) aluminum in the context of die casting. The cost of extracting pure aluminum for casting processes is extremely high, so it makes sense that most aluminum sources are recycled.
Secondary aluminum alloys are derived from mixing and melting pure aluminum with other materials such as magnesium, iron, and copper. Additionally, secondary aluminum is more economical to produce as compared to primary (pure) aluminum because it only requires about 5 percent as much energy to produce. Most of the energy consumption in aluminum die casting is used to heat and reheat the metal during fabrication, and for this reason, metal casting companies like Protocast are able to save more time, energy and money by re-melting aluminum alloys in-house.
Here’s a quick recap of aluminum alloy characteristics:
- High operating temperatures
- Outstanding corrosion resistance
- Extremely lightweight
- Very good strength and hardness
- Good stiffness and strength-to-weight ratio
- Excellent EMI and RFI shielding properties
- Excellent thermal and electrical conductivity
- Ideal finishing characteristics
- Fully recyclable
Casting With Magnesium
While Protocast Inc. specializes in casting and machining with aluminum alloys, our Denver machine shop also works with magnesium casting technology for structural applications. Magnesium castings have experienced great strides in development since 1921 when the Dow company began producing magnesium pistons. Magnesium casting technology was well developed during and after World War II and included both gravity sand casting and permanent mold casting in addition to high-pressure die casting. The primary applications for casting with magnesium revolved around the aerospace, defense and automotive industries, similar to that of aluminum. The alloy ‘AZ91D’ is the most widely used magnesium die-cast alloy and has an excellent combination of mechanical properties, corrosion resistance, and overall castability.
Unique Properties Of Magnesium
In the last 20 years or so, most of the development around magnesium casts have been focused on thin-wall die casting applications in the automotive industry. By taking advantage of the superior castability of magnesium over other metal alloys, companies are able to save significant amounts of money and time in their manufacturing operations. Without getting too technical, it’s important to note some of the unique solidification characteristics of magnesium. These include things like excellent fluidity and less susceptibility to hydrogen porosity, and thus, better castability over other cast metals like aluminum and copper. For all magnesium-based components brought to market, casting is the dominant manufacturing process – in fact, about 98 percent of all magnesium structural applications are done through one casting process or another.
Magnesium Processes
High-pressure die casting is typically the most common processes used for casting magnesium alloys, and several variants of this process have been and are being developed to improve casting properties. For high-performance aerospace and defense components, gravity sand and permanent mold processes are used. Emerging processes that have been developed and refined in recent years include things like low-pressure casting, squeeze casting, semi-solid casting, lost foam casting and ablation casting.
The Widespread Use Of Magnesium In Today’s Evolving World
Our planet and modern society at large is constantly facing the need for lightweight, energy-efficient and environmentally-friendly engineering systems and solutions. This need for improved engineering methods is driving the development of a wide range of structural and functional materials for energy generation, energy storage, propulsion, and transportation. While inherently challenging, magnesium, the earth’s eighth most common element found in the crust, offers promise as a versatile casting metal.
Such as the case with aluminum, the ease of recycling as compared to conventional polymers makes magnesium alloys environmentally attractive. As the machining and casting industry nears 100 years of technological and systemic development, magnesium casting processes are set to help meet the increasing demands for lightweight structural systems, particularly in the automotive industry.
Here’s a quick recap of magnesium alloy characteristics and benefits:
- Lightest of all structural metals
- Excellent stiffness and ideal strength-to-weight ratio
- Great EMI and RFI shielding properties, like aluminum alloys
- High electrical and thermal conductivity
- Can withstand high operating temperatures
- Good environmental corrosion resistance
- Cost-effective as compared to many engineered thermoplastic materials
- Exceptional thin wall capability
- Full recyclability
Casting With Zinc
Finally, we come to the other metal alloy that we work with – zincl. Zinc’s high strength and hardness lends itself to many solutions, ideal for machined, pressed, stamped and fabricated components.
Additional Applications
Similar to that of aluminum and even magnesium, complex net-shaped zinc housings make for precise, thin walls that offer excellent electrical performance and shielding properties. As such, this makes zinc as a great choice for a broad range of consumer electronic devices. Like stainless steel, the castability, wear resistance and structural integrity of zinc make it an ideal alloy for the creation of multi-faceted, highly-complex shapes. These shapes are typically used in automotive safety applications as well as the electronics industry.
Engineering Support And Machined Parts
By specializing in non-ferrous alloys, Protocast Inc. can offer rapid prototype casting to production casting, getting the job done right every single time. In our industry, precision is key and there’s absolutely no margin for error in our work. Many of our employees at our Denver-based machining foundry hold engineering degrees, meaning that our engineering department can help you support projects large and small. From basic feedback on casting and machining intricate parts to reverse engineering, 3D CAD modeling, and Computation fluid analysis, there’s a solution that we can provide for you and your company.
As we’ve covered above, there are times when cutting a part from stock is the only economical way to produce it. Therefore, our full-line machine shop is staffed with engineers and operators who are capable of producing the highest quality parts you can possibly obtain for your production.
Toolmaking And Part Modification
As opposed to a matter of months, Protocast Inc. can cut matchplate tooling in a matter of weeks, saving your production time and money. To make this possible, we have three dedicated CNC machines that execute tool cutting operations. For a part that needs to be updated, is becoming obsolete, or simply doesn’t work the way that it’s supposed to, our part modification services can help.
Ensuring Quality And Precision Every Step Of The Way
By inspecting and testing everything we do on-site through a variety of tools and machinery, we ensure that your parts, tools and other components are manufactured to your exact specifications, and we won’t accept anything less than what you’re looking for.
Where else can you find a comprehensive foundry like Protocast Inc. in the Denver area? As our home, we’re proud to serve you and your company in Colorado and beyond. For precision engineering, trust our prototype casting services. Learn more about Protocast Inc. here!