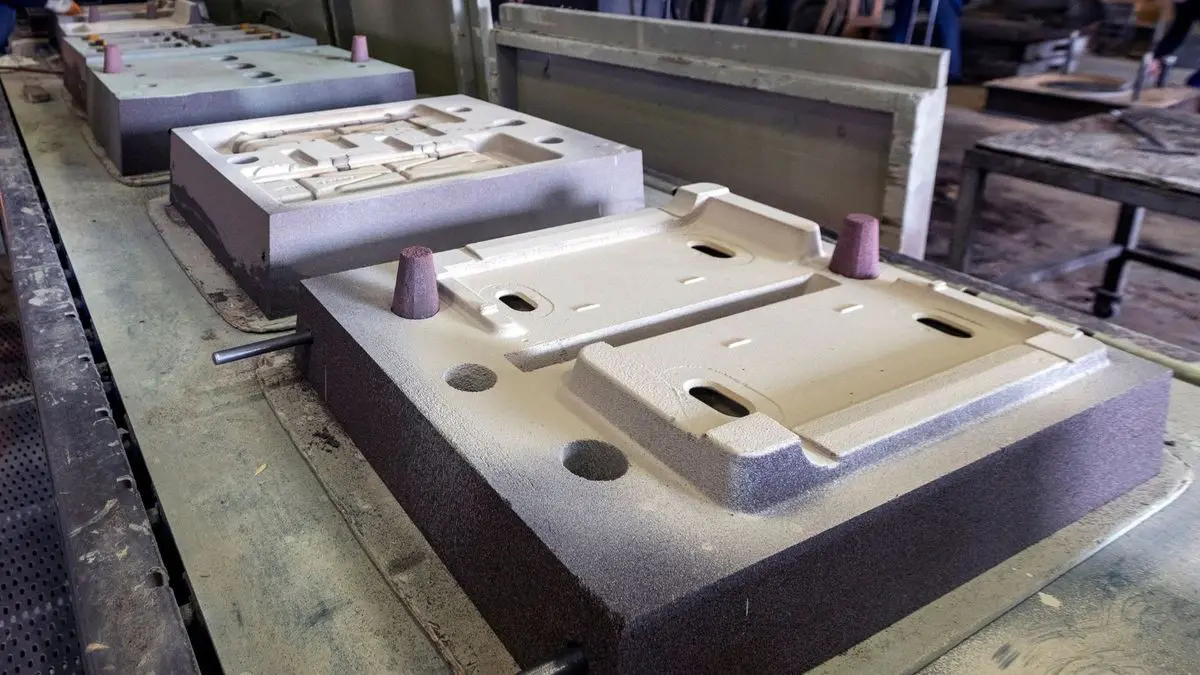
January 26, 2023 | Prototype Casting
Why You Should Choose Sand Casting For Your Machine
Sand casting is an incredibly versatile production process that has been utilized for centuries to create machine parts with complex designs. It is one of the oldest casting methods and remains a popular choice today due to its affordability and impressive results. At Protocast, we specialize in forging the highest-quality metal components for a myriad of industries and uses. Our mastery of sand casting is unparalleled, offering a plethora of advantages for our customers. Below, our team has delved into why sand casting is an ideal solution for your machine parts. Read on to learn more about how our team harnesses this method to achieve exceptional results, and schedule an appointment today!

Sand Casting Is Versatile
It’s important to note that sand casting is a versatile process that can be used to create a wide range of shapes and sizes. Whether you need a single prototype or a large production run of parts, sand casting can accommodate your needs. Our precision sand casting process, which uses fine-grain sand combined with a two-part urethane binder, allows us to produce high-quality parts in as little as three days.

Strength & Durability
Because the process allows for larger castings with thicker walls, parts produced using sand casting tend to be stronger and more durable than those produced using other methods. Additionally, our precision sand casting process achieves a surface finish of approximately 200 microinches, which is significantly better than green sand castings.
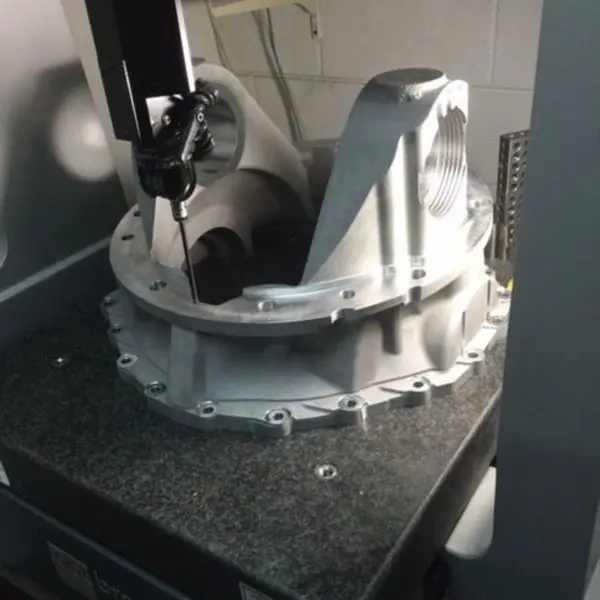
Dimensional Tolerances
Our use of ESI Quick Cast Computation fluid analysis and FEA software allows us to simulate casting solidification and make sure that the final product meets your exact specifications. Furthermore, our in-house machine shop allows us to finish the parts and make sure they meet your requirements.
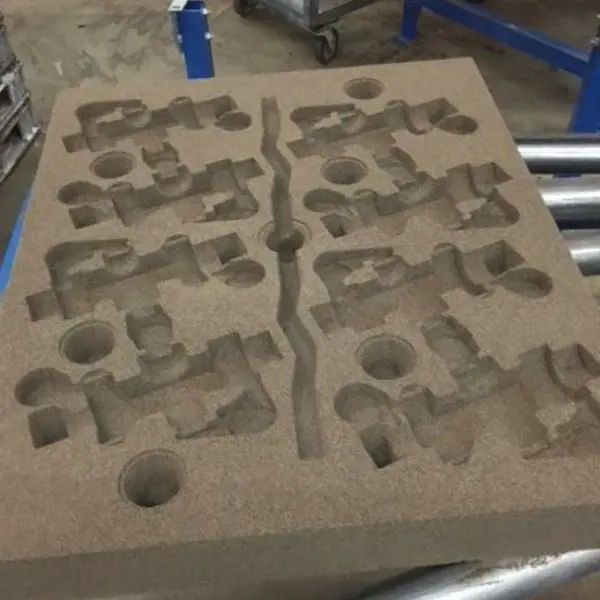
No Need For Hard Tooling
Our recent foray into 3D printing technology has enabled us to introduce a revolutionary printed sand mold procedure that has eliminated the need for hard tooling. This has opened up the doors for us to craft complex geometries that were previously confined to production investment casting and yield a limited selection of sand molds in just five days from purchase.