Protocast Inc.
Offers Rapid Prototype To Production Castings For A Wide Variety Of Industries.; Specializing In Non-Ferrous Alloys.
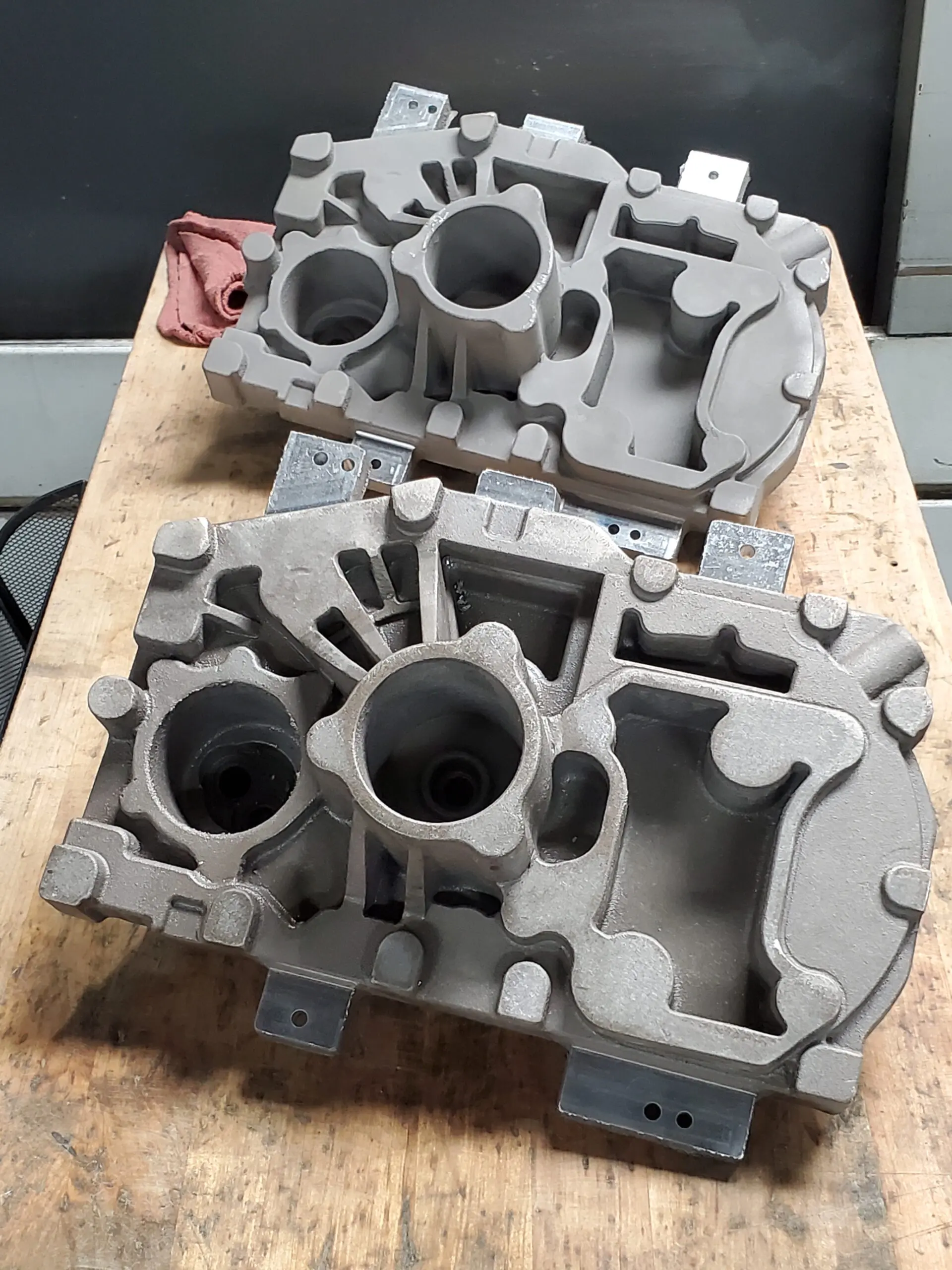
Precision Sand
Nearly half of our employees hold engineering degrees. From basic feedback on casting and machining, to reverse engineering, 3D CAD modeling, and Computation fluid analysis, our engineering department is capable of supporting projects large and small.
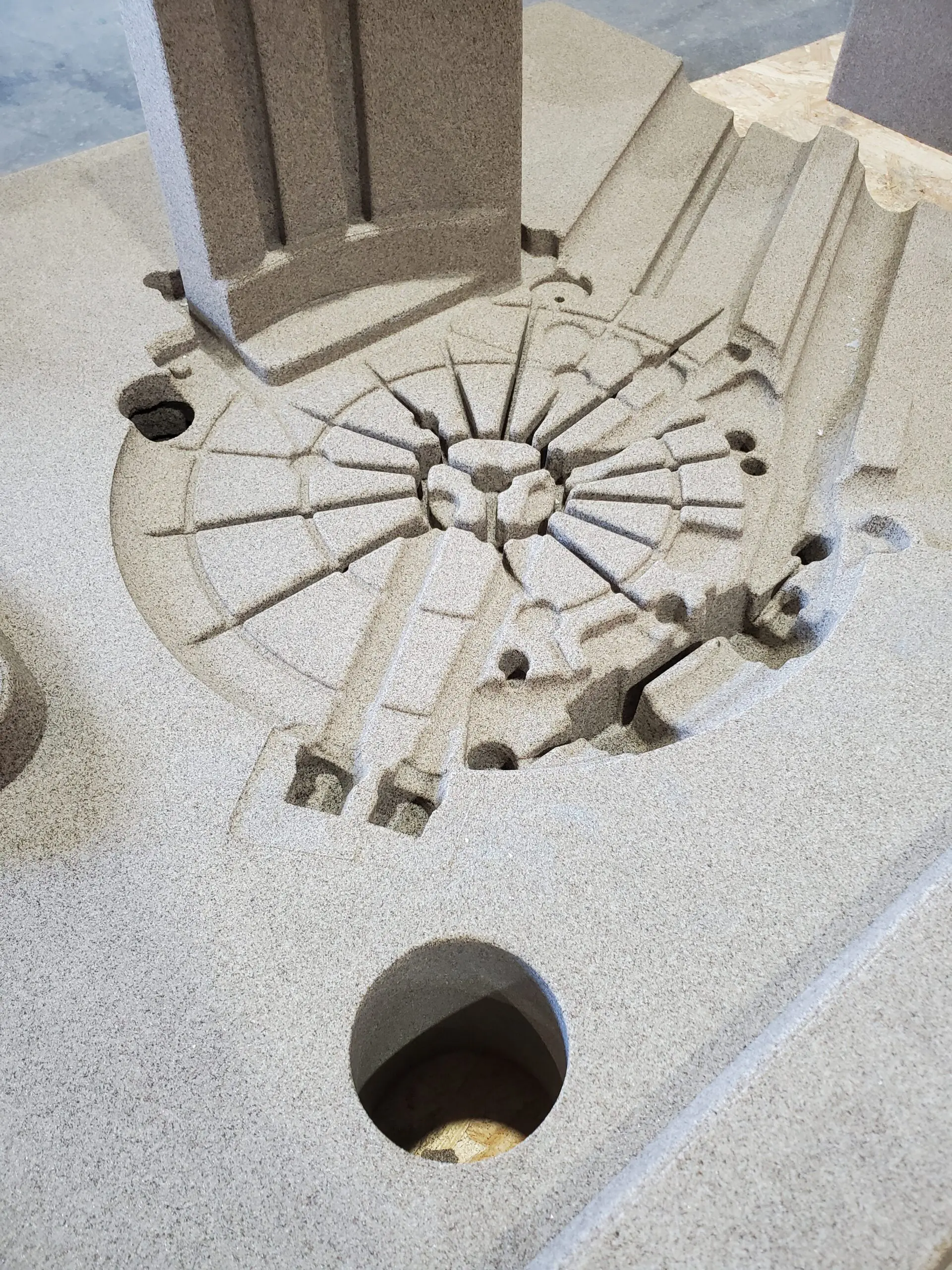
Printed Sand
There are times when cutting a part from stock is the only way (or most economical) way to produce it. Our full-line machine shop is staffed with both engineers and operators who are capable of producing the highest quality parts.
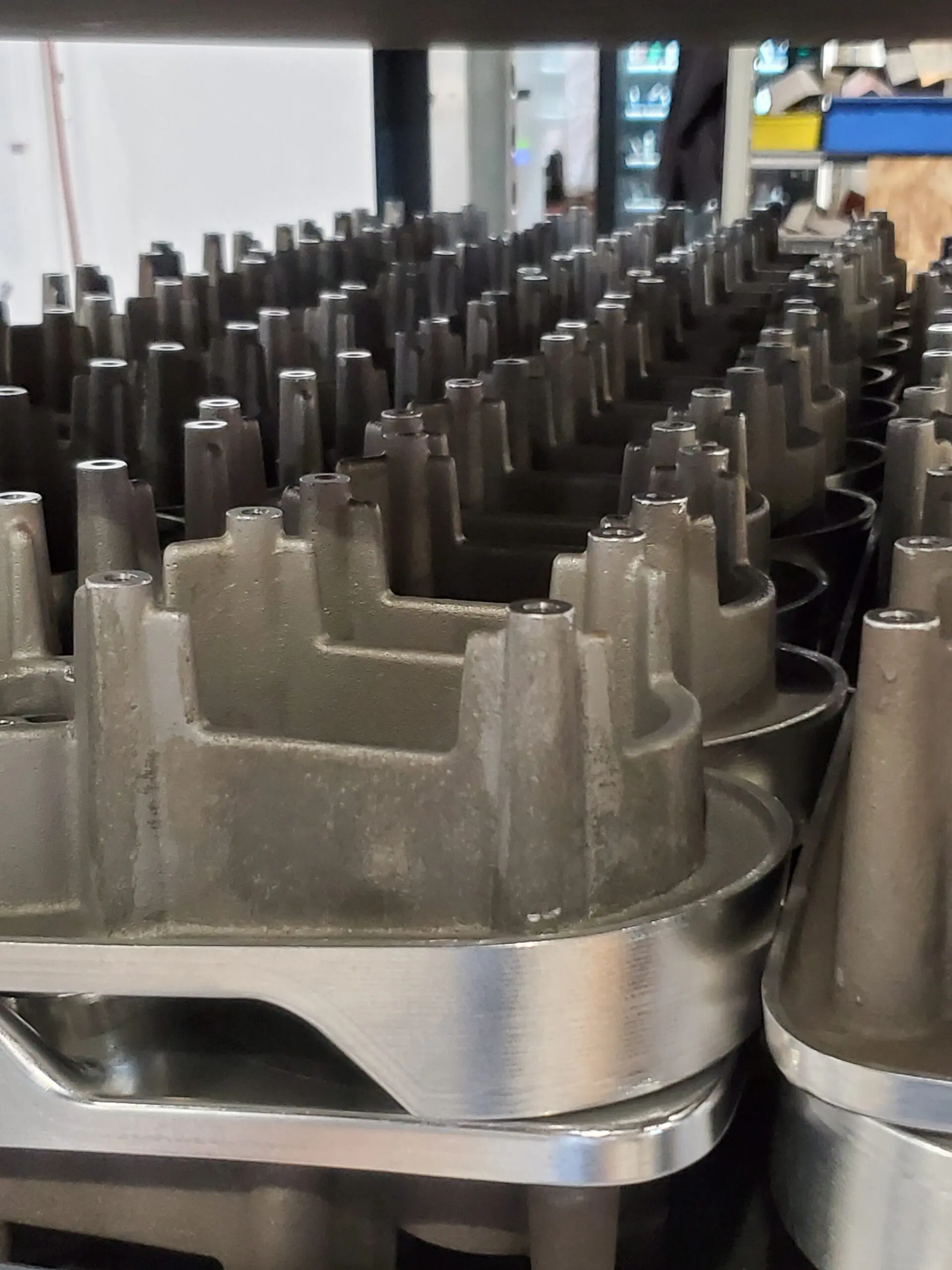
Die Casting
With an in-house CMM, we can perform most dimensional inspections on-site. We have experience with variety of customer defined pressure and leak tests as well. Additionally, we can send parts out for x-ray, dye penetrant, tensile test bars, and other testing services.
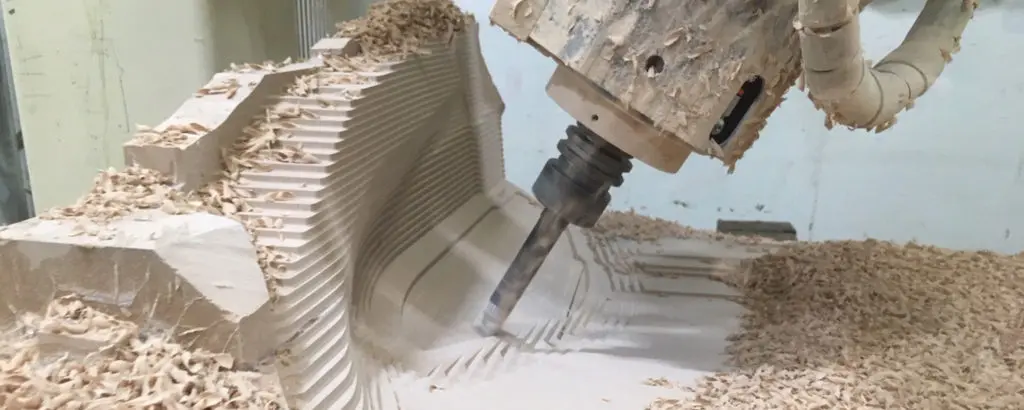
Toolmaking
If the foundry you typically use is experiencing longer than normal lead times, we can often engineer and cut matchplate tooling in a matter of weeks instead of months. We have 3 CNC machines dedicated to tool cutting operations.
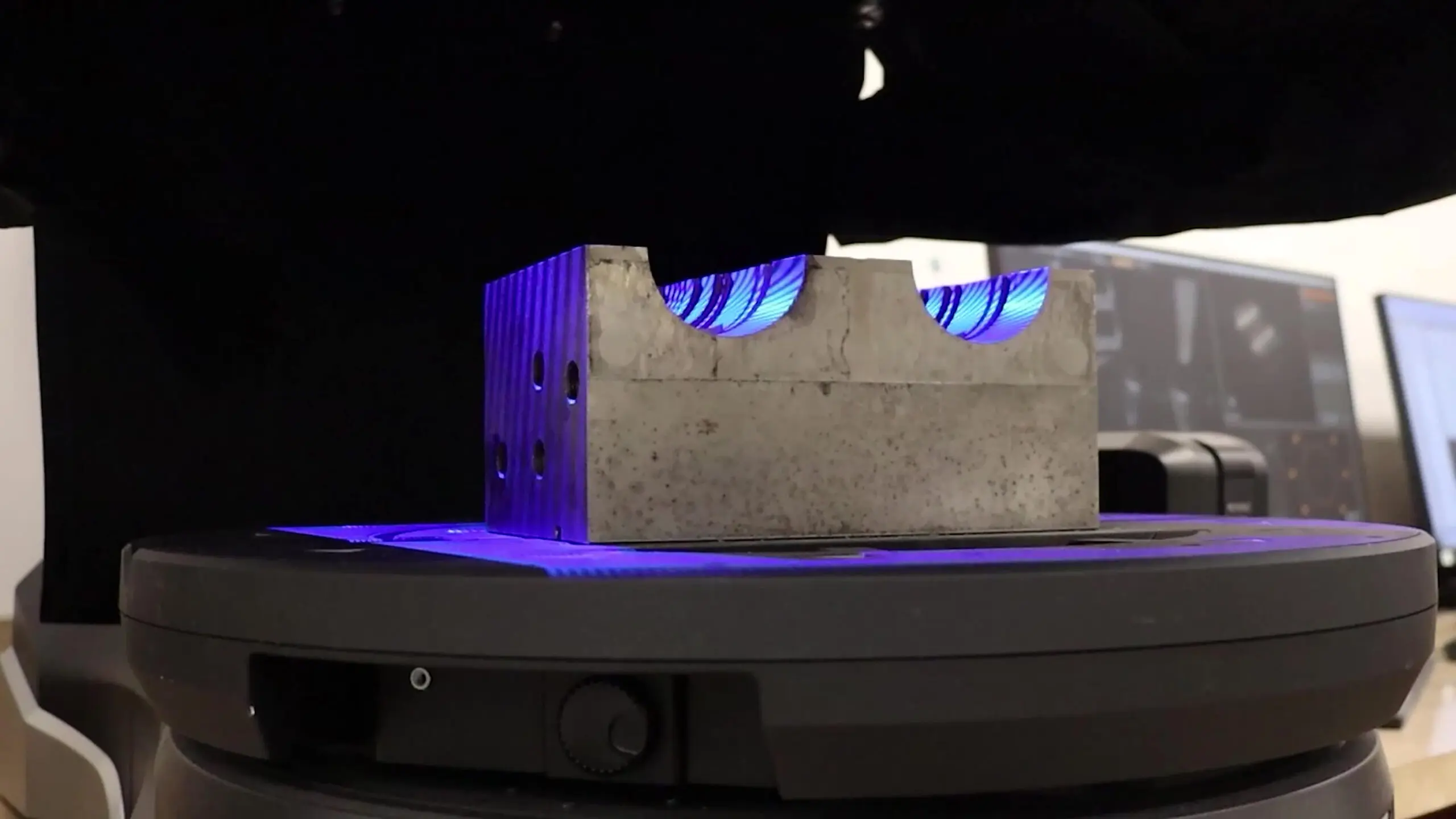
Part Modification
Sometimes a part needs updated or is going to obsolescence, or simply doesn’t work the way it’s supposed to. For those times, you need a partner that can modify tooling or reproduce the part, repair old tooling, or modify it in a permanent way.
At Protocast Inc.
We offer Prototype to Production Casting & Machining, we specialize in providing our customers custom metal casting services for a wide range of applications and industries. We offer sand castings, permanent mold castings, die castings and investment castings just to name a few. We offer these services for aluminum, magnesium, and zinc castings.
Early involvement with our customers is an important step in the metal casting process. From a concept to the full production of a product, the staff and engineers at Protocast are ready, willing and able to assist you in exact design specifications. Let us be your metal foundry of choice.